The custom development by Torsa of a high-precision collision avoidance system for the shovels at Antamina has generated excellent benefits for the company’s operations and safety areas.
In August 2015, a relationship began between TORSA and Compañía Minera Antamina, initiated by TORSA presenting to the mining company its development capabilities and extensive experience in creating high-level technological systems.
Given TORSA’s extensive experience in developing RFID-based systems, Antamina offered to test this technology in its mining operation to help minimise the existing risks during loading activities and to reduce the number of incidents occurring in the interactions between shovels, trucks, and cleaning dozers.
After the initial field tests a few months later, both teams found that RFID-based technology alone was insufficient to meet Antamina’s primary objective.
To alert the operator to the presence of vehicles and obstacles within a 20-metre area around the shovel with centimetre-level accuracy.
The operators required a high-precision system that would inform them of the distances within their closest range of action, from 0 to 5 metres from the shovel.
At that point, TORSA proposed to Antamina the joint development of a high-precision anti-collision system for shovels, with TORSA providing all the technological development.
TORSA deemed it absolutely necessary for the system under development to meet the following criteria:
- Robustness: the system had to offer a high level of protection to withstand the demanding mining environment—located over 4,000 m above sea level in the Andes mountain range—and to endure continuous exposure to dust, mud, electrical storms, rain, hail, etc.
- Precision: the system needed to deliver high accuracy to alert shovel operators to existing risks, as it was determined that a reliable warning required at least 10 centimetre precision.
- Reliability: the system must produce zero false positives; it had to be completely dependable to ensure the safety of both the operator and the vehicle, since false alarms would undermine operator trust.
- Cost‑effectiveness: it was also essential that the system be economically viable in order to recoup the investment.
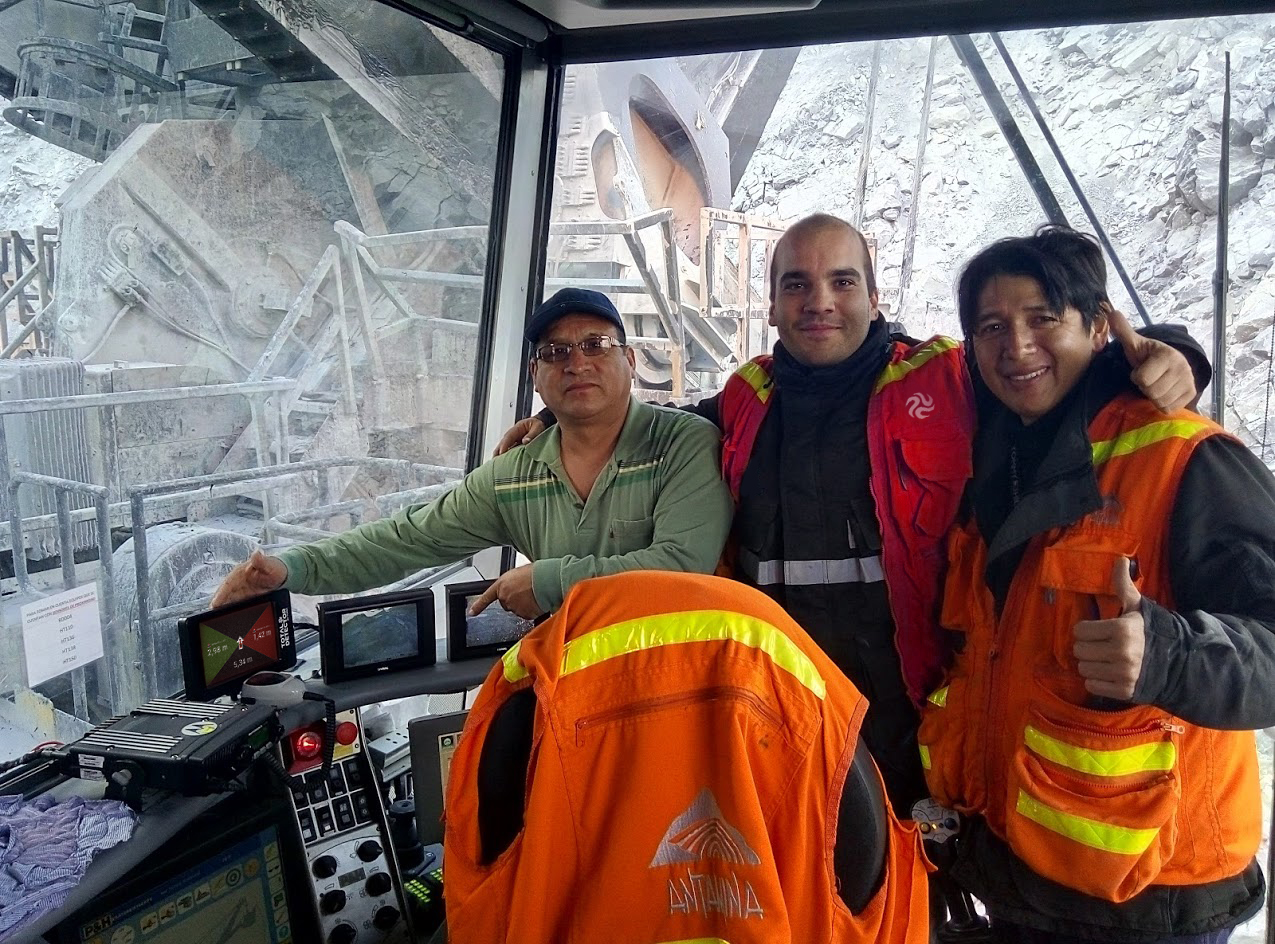
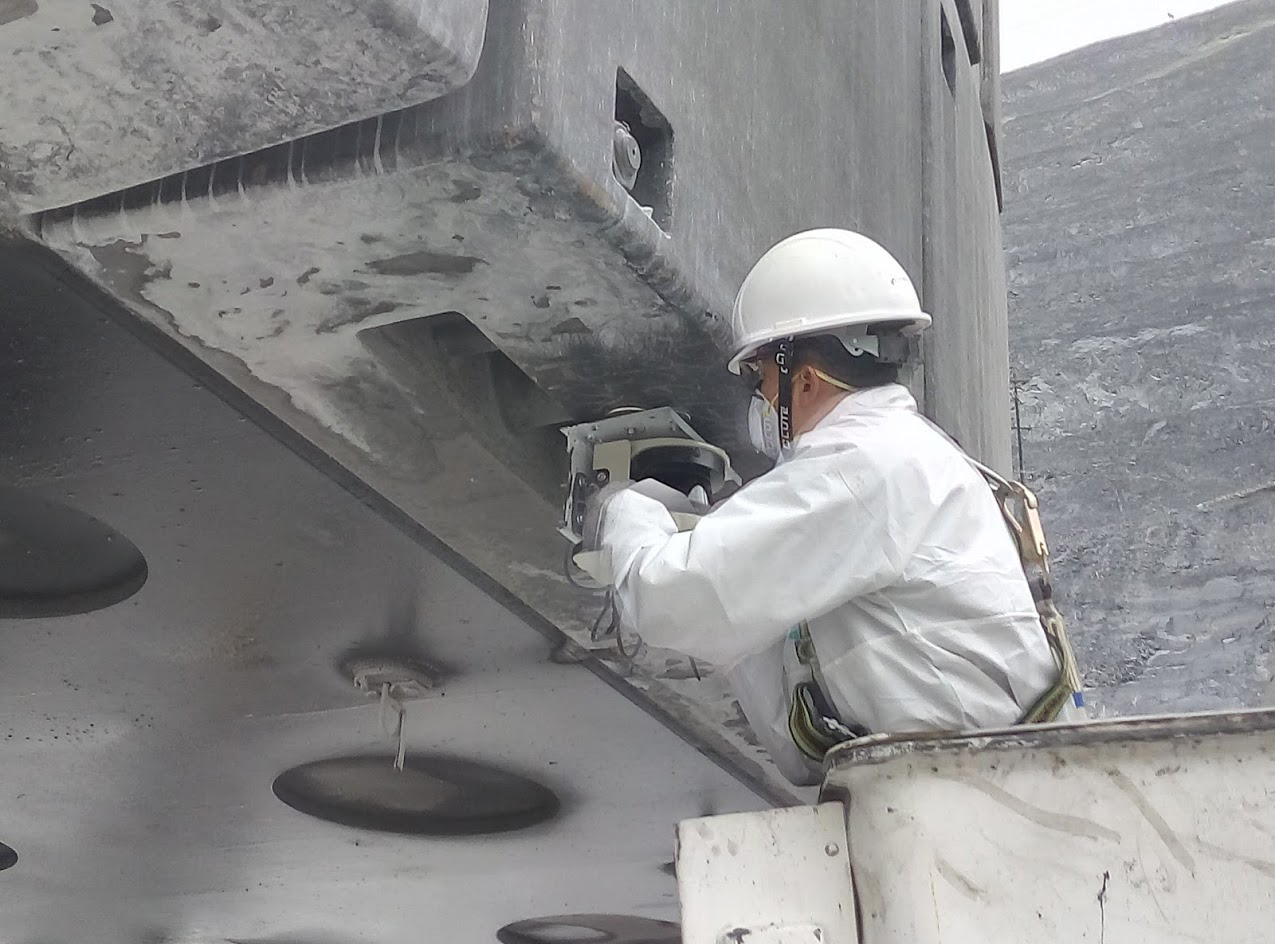
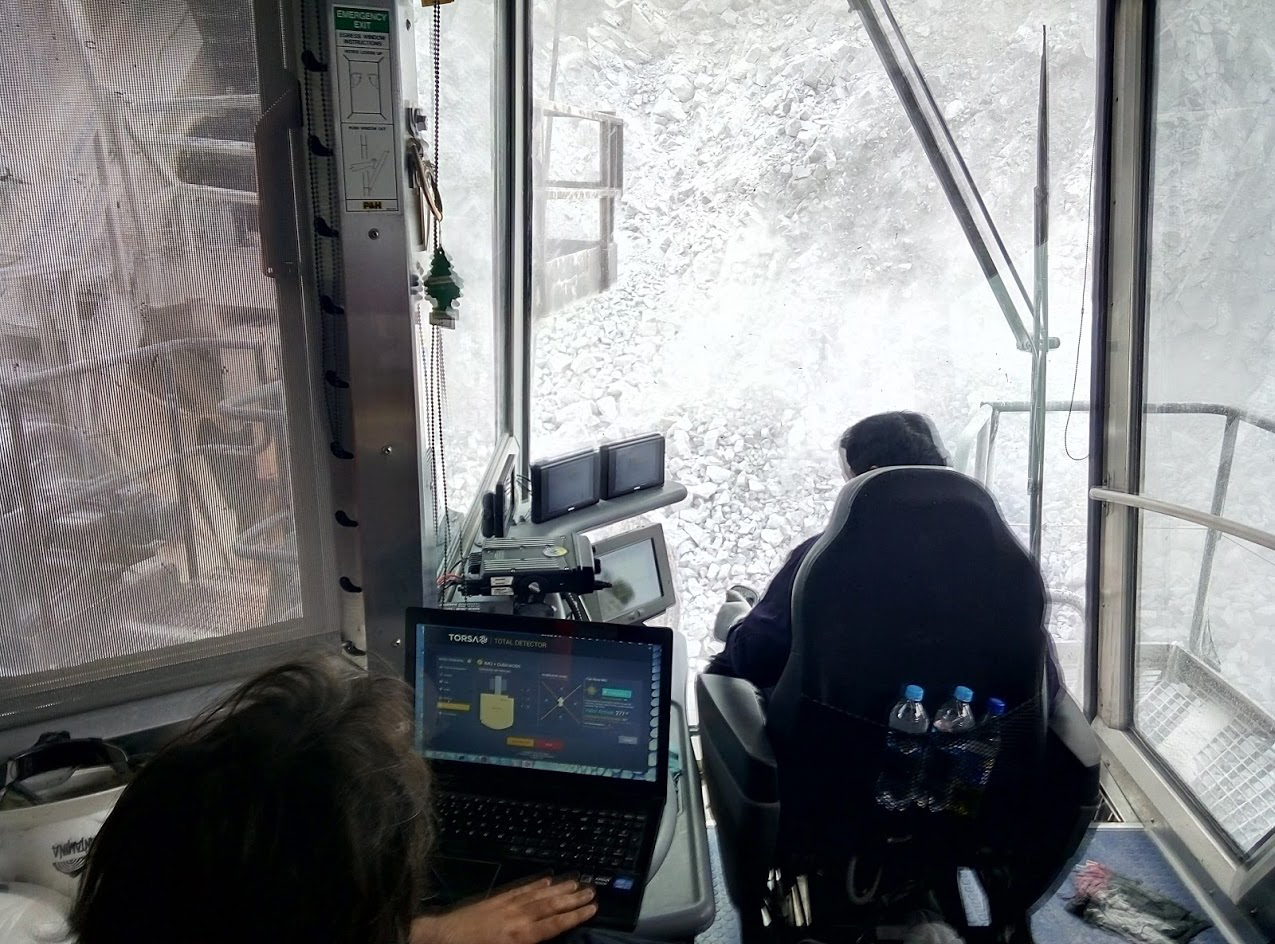
In just six months from the time the system was proposed, and after a great many hours invested in research, study, and development, TORSA was able to design all the hardware, software, firmware, and detection algorithm for an entirely new system ready for deployment and field testing.
The system, which was originally based on radio‑frequency detection, evolved into a new sophisticated solution leveraging high‑precision technologies (LIDAR, RTK GPS, etc.), with a complex detection algorithm capable of mapping the entire working environment of the shovels and alerting operators in real time with 1‑centimetre accuracy.
After a two‑month pilot test, the system was approved by Antamina, which decided to install it on all its shovels, and it has been operating ever since to the great satisfaction of the mine’s operators.
Additionally, the system was equipped with a powerful communications interface that sends all detection data and system events to the .torsacloud platform for continuous analysis and monitoring from Antamina’s control center.
Conclusions
During the pilot test, TORSA personnel were able to interview all the shovel operators involved in the trial and adjust various aspects (alert sounds, user interface, etc.) to ensure their comfort and safety. TORSA’s high‑precision shovel system was able to accommodate all the needs expressed by the operators, since as direct users of the system it was essential to ensure that it was not invasive and that it alerted them at all times whenever a risk was detected in their operational area.
The system was designed to enhance the safety of the mining operation during loading and vehicle interactions, but after its rollout across Antamina’s entire shovel fleet, it was observed that the system also significantly benefits operational productivity. By increasing safety and giving operators greater confidence, the number of trucks loaded per hour rose substantially. A field study determined that, after system implementation, shovel operators loaded an average of 2.5 additional trucks per hour.
NATIONAL TECHNOLOGICAL INNOVATION AWARD 2019 (PERU)
The National Society of Mining, Petroleum and Energy of Peru (SNMPE) has awarded the 2019 Technological Innovation Award to TORSA and Compañía Minera Antamina for the custom development of the high‑precision anti‑collision system for shovels. The project was deemed a success due to the drastic reduction in equipment‐interaction incidents, enhanced safety during loading operations, and the increased productivity achieved.
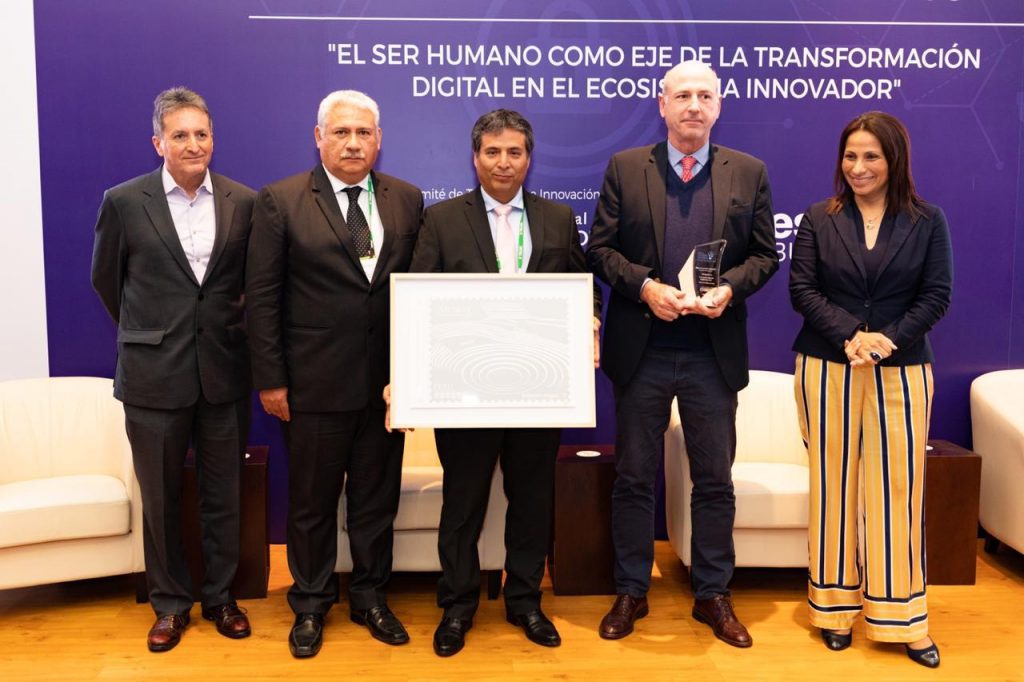